Engineering your business
Back in 1995, 20 years ago, I did an Associate Diploma in Industrial Engineering when I first left High School.
Being a wide eyed 19 year old, I did not really know what I was getting myself into, in fact I thought Industrial Engineering was something to do with Industrial Design which I was quite good at in high school. But I was wrong, very wrong.
Little did I know that Industrial Engineering is actually about the optimisation of processes, systems or organisations. That industrial engineers work to eliminate waste of time, money, materials, man-hours, machine time, energy and other resources that do not generate value. According to the Institute of Industrial and Systems Engineers, they figure out how to do things better, they engineer processes and systems that improve quality and productivity. – Source Wikipedia. Little did I know that the skills I was learning would be so valuable to me in small business many years later. In fact I had no idea how I would ever apply them, but I did not want to give up on something that I had started.
Another weird thing was that the Associate Diploma of Industrial Engineering was only offered at the Hunter Tafe for 3-4 years to support manufacturing industries in Newcastle at the time so the course was ended just after I got my Associate Diploma.
Typically Industrial Engineers are employed by large blue chip corporations, think Samsung, General Electric, Apple, Johnson & Johnson etc. In fact did you know that Tim Cook, the head of Apple, the most successful company on the planet is a qualified Industrial Engineer. However, that being said there is nothing stopping Industrial Engineers from working in small business or even micro business. For example a project I remember working on back in my Tafe days was where we had to study how you would toast bread and work out the optimum way that you could efficiently toast bread by studying the toasting process through Industrial Engineering techniques and tools such as Modapts. So if you can optimise Toast, you can optimise any process. Let’s face it, a process is just a series of steps for someone to get from A to B and a small business is filled with hundreds of processes.
In this article I will touch on how I have used Industrial Engineering, the diploma I had no idea what to do with, to engineer and optimise my design business.
Quality Control
Quality control (QC) is a process by which entities review the quality of all factors involved in production. –Source Wikipedia
So QC is basically the testing of a product before it goes to a customer. All companies who produce something should do this. While I don’t produce a product it is still very important to check my work and test the functions on websites. If I were to send something off to be printed that contained a fault (i.e. spelling mistake, wrong phone number etc) it could result in a costly mistake as I would need to provide reprints. It may mean a customer does not receive their product on time and in the long term loss of business for me as many of my jobs are referral based.
To help with my quality control I have a checklist and process flow chart. So before I finalise a job like making a website live I check it over thoroughly. I go through a checklist I have compiled for the job to make sure I have included everything the customer has requested, and I go through my process flow chart and it is not until I am satisfied with the quality of the work, that I then set it to go live.
I expect QC from businesses I use too. The business that I use to print my work needs to make sure their equipment has done the job at a high quality. The coffee shop I go to needs to put the right amount of sugars in my coffee. The computer I use needs to turn on every day. I’m sure all these places have a means of quality control. The print shop looks at the work to see it’s printed properly, the coffee shop double checks the order to make sure it has been made correctly, the computer place tests each computer to make sure they are in working order and that is only once a prototype has been proven to work and last the distance. If they failed at their quality control I would stop using them.
Think of all the big brands out there, they are big because they have continued to make quality products and have built a strong name. I buy products because I know the brand that makes them are of high quality, and this comes down to their quality control.
Quality Assurance
Quality assurance (QA) is a way of preventing mistakes or defects in manufactured products and avoiding problems when delivering solutions or services to customers. –Source Wikipedia
So while quality control is checking the quality of each product produced, quality assurance in maintaining that desired level of quality through different processes. A quick example of this is the coffee shop. While QC is checking the final order is correct, QA is the processes that have been set in place to make that coffee the best it can be. The machine used, the brand of coffee used, the brand of milk used, the person who makes it is qualified… all the processes that have been put in place and are known to come together to make a nice, quality beverage.
While I do not ‘manufacture products’ per-say, I have again been able to apply the concept to my business of branding, graphic design & web development. I have set processes in place to maintain my level of communication with customers and make sure attention to detail is payed with each customer or project I am working on. This helps maintain a level of quality, and also saves time. So I have a generic email sent to new customers, a generic quote I can customise for work, a set of steps I follow for each new job, I even have a generic email to go out for overdue accounts. Once I was happy with the quality of these documents I was able to confidently and quickly send them out, enabling QA.
I also use procedures to enable QA too. Each time I set up a new website I have a procedure I follow and a list of things I use for each website I design. I do this because I know what apps I like to use and what plugins work. Having the procedures in place means each time I set up a new site I can follow the steps ensuring I don’t miss or forget an important factor. If I was swapping and changing these details for each new website I could run into many problems, it is these processes that give my business quality assurance and I can produce quality work. Using procedures also allows someone else to walk in and set up a website or send a quote efficiently. I can then check this later on as part of my quality control.
Time Management
Time management is essential for the growth of business. If I took a month to finalise just one job then I couldn’t grow my business, or even afford to maintain my business. To assist me with time management I use timesheets. Timesheets help me to stay on track and see how long jobs take me to complete. To be able to tell a customer I can complete a job by a deadline time management is essential. To grow my small business I must be able to take on more work, and this also comes down to time management.
I have also analysed my timesheets to optimise my business. Basically I analysed my timesheets in great detail using spreadsheets and graphs and worked out how I could get more time for my business and less time on things that were not growing my business like admin. I used the information I found to set up more processes and increase my productivity. Read more about the Hidden Value Of Keeping Timesheets here.
Just in time manufacturing
Just in time manufacturing is a methodology aimed primarily at reducing flow times within production as well as response times from suppliers to customers. –Source Wikipedia
While my business doesn’t manufacture products that are needed just in time I have applied this methodology in another area of my business. I call it Just in Time Learning. This is the process of utilising the internet and it’s resources to learn what is needed when it is needed. So if I were to use a new app that a customer had requested and I can’t find my way around it, a simple YouTube video or web search would have me getting the job done in no time at all. I can take on work with no hesitation as I know the answers to all my questions are on the World Wide Web.
Continuous Improvement
Another keystone of Industrial Engineering is the Japanese philosophy of Kaizan, which translates to change for the better or continuous improvement. This has evolved into a business philosophy which applies continuous improvement in the areas of efficiency and quality. This means that businesses do not have to feel they need to get from A to B in one large step but rather through many, many little steps. As long as you are changing your processes, systems, products and services a little at a time for the better, Kaizan states that over a long time the business will look dramatically different from when it started. A side benefit to this philosophy is that you can tweak the business to quickly move in new directions if necessary.
In Summary
When I started the Industrial Engineering Associate Diploma I thought I’d made a bit of a mistake and for a while believed it was a waste of my time as it wasn’t what I wanted to do with my life. Now I look back at it as one of the best mistakes I made. My business owes a lot of it’s success to that Diploma and what it taught me about optimising my business.
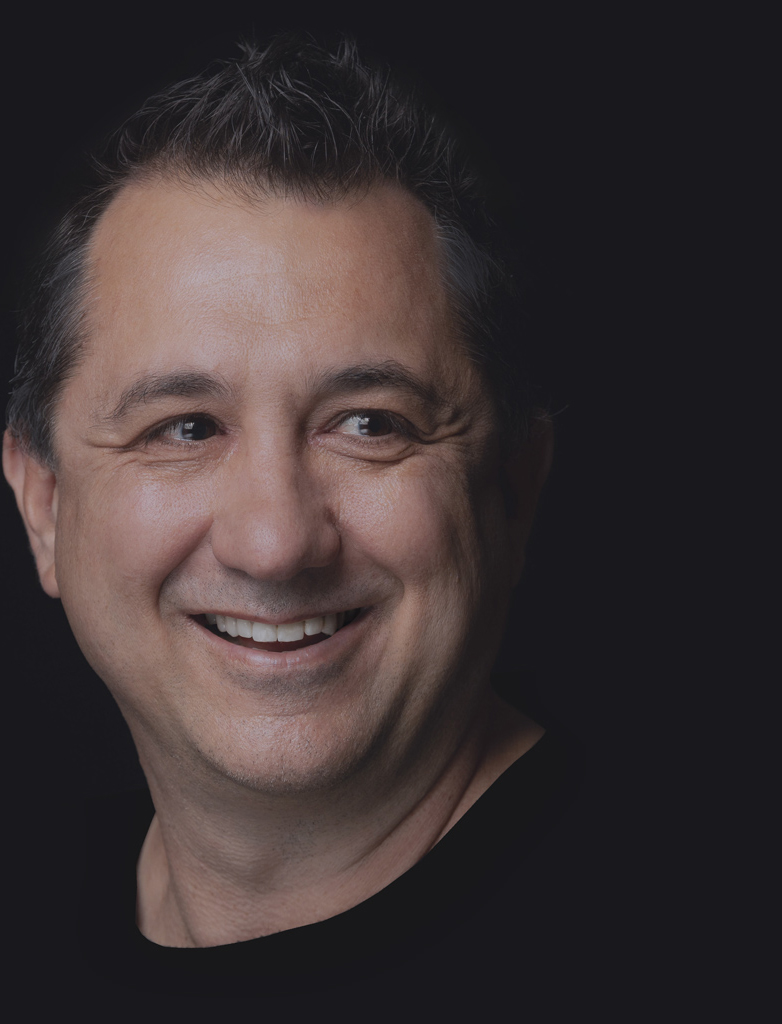
Daniel Borg
Creative Director
psyborg® was founded by Daniel Borg, an Honours Graduate in Design from the University of Newcastle, NSW, Australia. Daniel also has an Associate Diploma in Industrial Engineering and has experience from within the Engineering & Advertising Industries.
Daniel has completed over 2800 design projects consisting of branding, content marketing, digital marketing, illustration, web design, and printed projects since psyborg® was first founded. psyborg® is located in Lake Macquarie, Newcastle but services business Nation wide.
I really do enjoy getting feedback so please let me know your thoughts on this or any of my articles in the comments field or on social media below.
Cheers Daniel
Great post Daniel,
I totally get where you are coming from, I also totally know these are areas of my business that are under done. As an architect, much like other designers, processes and procedures seem boring and not very creative. As I work with many Engineers, I always admire their discipline they have.
Now off to read the Hidden Value of Keeping Timesheets, kinda critical to what I do, but do not spend the quality time in analysis (another engineering thing).
Thanks again for the post.
Thanks David.
Yes, I agree, these can be quite boring tasks but once they are in place you do not really need to do them again and you can only improve on them as you implement them.
As a creative, I find that implementing these systems can actually help to be more creative as they take some hassle and worry out of the design process freeing me up to think differently where required. It’s a way of setting up some limitations or boundaries to the creative process.
Hey David, love your comment. Text me (0414 914 087) your T-Shirt size and address and I’ll get a psyborg tee in the post to you.
Great article Daniel. Engineering your business is so crucial to having a scalable business as well as delivering great service. Love how you have explained these principles.
Hi Steph – thanks for your comment and yes, scaling the business will be the true test of these systems which I am sure will provide opportunities to further refine.
Hello Daniel
Since retiring from work I have found that I am not a self starter. Once I am in the habit of doing things I continue to do them. But I can’t establish that habit myself.
(I guess I am a bit like a motor car – I need someone to turn on my starter key first)
I have found from my at work days that once what I have to do is established I continue to do it.
Could you offer me a technique that over time will allow me to develop my own self starter habits in a way that will be long lasting.
As well as things I do in my personal life I have commitments – that have deadlines- with the two Toastmaster clubs I am involved with plus Folk Club administration work.
So I really do need to be able to set up and maintain a system by which I can do everything I need to do within time limits. But currently when I try to establish this, I start on one item and then tend to concentrate on it and not leave the required time for other items.
Hi Trevor, I think most people have the same issue so you are not alone. What you are referring to is how to make a ‘change’ beyond your regular patterns of behaviour. For each new change you are referring to, I think you have to imagine the reward or benefit which that change will make to your life. This means you need to vividly visualise it so that you clearly understand the benefit. This could mean imagining it over and over again so that you get quite comfortable with the reality of it. The great thing about doing this is that it takes little effort ‘imagining’ and before you know it your mind will start compelling you to do it, before you know it you will be motivated to make the changes necessary that you were just imagining.
Also as you alluded to once you start doing these things you need a way to manage them so that you can stay focussed and on track with them. The most practical way I know is to monitor the tasks through some kind of timesheet system. This does a few things for you. First it allows you to become more aware of the work you are putting in on task, thus re-affirming the importance of the tasks so you will be more obliged to take it up again, and secondly it allows you to start looking at what you are doing from a birds eye point of view so that you can start re prioritising and removing tasks. I have actually written another blog article on this topic. Check it out here – https://www.psyborg.com.au/lean-and-agile-office/hidden-value-timesheets/
I hope this helps.